A roll former is a machine that may seem tremendously complex, with its various stations and high speeds. However, understanding how it works is valuable as it can perform a unique function, consistently creating identical end products that meet the strictest specifications.
To better comprehend the roll forming machine's operation, it's beneficial to break it down and study each place where the metal undergoes some change—whether it's bent, punched, cut, or folded.
Roll Form Tooling
Whenever sheet metal undergoes a change on a roll forming line, the roll former's tooling progressively alters the metal's shape. Starting as a coil, the metal undergoes various changes before becoming a finished product at the other end.
Forming is carried out by tool steel rolls rolling over the work metal. Each roll successively changes the shape of the sheet metal as it advances on the line. Increasing the bend progression too fast can damage the material, while too slow progression requires extra dies or forming points, making the machine more expensive and space-consuming.
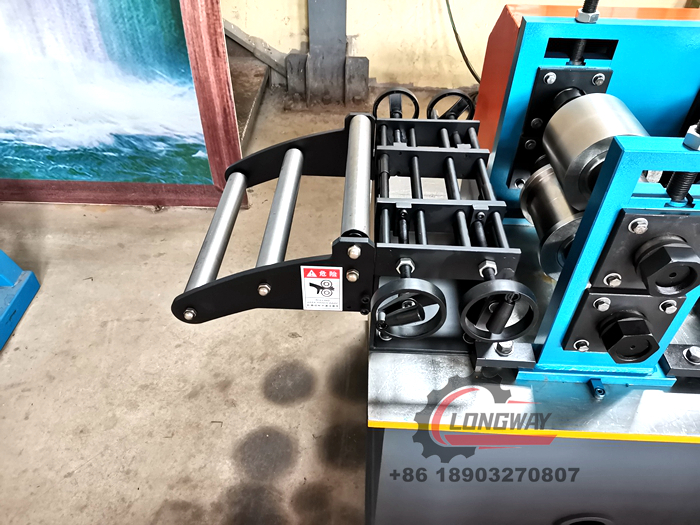
Metal Roll Forming Punching and Cutting
A roll forming line can form, punch, and cut various metals in different gauges for use in industries like construction. Deciding whether to punch the metal before or after forming is crucial, as it affects the end product.
Cutting the sheet metal at a specific point on the roll forming line is important, and the location of the cut influences the final product. Fabricators must account for flare and understand how forming affects it.
Roll Forming Tooling
Anytime sheet metal is changed on a roll forming line, it is done by the roll former's tooling. Forming occurs as the sheet metal rolls under each steel roll, changing the metal's shape successively. The top roll impresses indentations, and subsequent rolls deepen these impressions and begin to curve the raised sections.
Weighing the differences between precut and postcut operations can help determine the best approach.
Precut Pros
- Eliminates expensive cutoff dies and maintenance.
- Results in burr-free ends.
- Uses a simple, low-maintenance precut shear.
- Allows hand feeding for low-volume production.
- Prevents cutoff distortion.
Precut Cons
- Can increase end flare, especially in deeper parts.
- Necessitates more overbend in high-strength steels.
- Requires more forming stations, making it more expensive.
- Generally needs more floor space.
- Makes controlling quality in multibend parts difficult.
Postcut Pros
- Raises production rate as the uncut coil runs continuously.
- Facilitates better part control, reducing end flare.
- Achieves better results for high-strength steels.
- Produces shorter lengths.
- Allows the use of end straighteners.
- Eliminates leading-edge deformation.
- Extends roll life on heavy-gauge and high-strength material.
- Friendlier to material gauge and hardness deviation.
Postcut Cons
- Can cost more initially.
- Adds maintenance costs.
- Causes end burr and rough ends.
- Creates distortion on product ends.
- May require manual feeding of the leading end when introducing a new coil.
- Requires all surfaces to be supported to avoid end distortion.
Metal Roll Forming Bowing, Camber, and Twist
Metal imperfections are common and can create problems during the roll forming process. Using tension-leveled steel or aluminum coil helps, and straighteners can be part of the line to address bow, camber, and twist.
Tooling Cooling
Roll formers operate at high speeds, and material heating can occur. Flood cooling extends tooling life but is messy, while dry cooling is cleaner but shortens tooling life.
Tooling Steel
Different materials react differently to roll forming stresses. The type of roll tooling steel and post-processes used on it vary based on the work material.
Rafted System
In a rafted system, tooling is preloaded on shafts, making profile changes more efficient and reducing mistakes. Rafted systems have advantages in reducing changeover times.
Metal Roll Forming Safety
Roll forming machines operate at high speeds, so understanding their built-in safety features is crucial. Keeping safety equipment in place and providing thorough training for operators is essential. Safety plans should cover the entire roll forming process.
Feel free to ask if you have any specific questions or if you'd like more details on a particular aspect!