PBR Roll Former Companies A Comprehensive Guide
Preface
PBR (Phenolic Butyrate Resin) roll formers are essential in the production of various plastic products. This article aims to provide a comprehensive guide to PBR roll former companies, including their history, key players, applications, and future trends.
History of PBR Roll Formers
The development of PBR roll formers can be traced back to the early 20th century when phenolic resins were first synthesized. Over time, these resins have been improved and modified to meet the growing demand for high-performance plastics. Today, PBR roll formers are widely used in the production of automotive components, electrical appliances, and consumer goods.
Key Players in the PBR Roll Former Industry
There are several major players in the PBR roll former industry, including
1. BASF A leading chemical company with a strong presence in the PBR market. Its products are widely used in various applications, including automotive, construction, and electronics.
2. Evonik Industries A global leader in specialty chemicals, including PBR. The company offers a wide range of PBR products for various applications, such as coatings, adhesives, and sealants.
3. SABIC A Saudi Arabian multinational corporation that produces a variety of chemicals, including PBR. The company's products are used in a wide range of applications, including automotive, construction, and packaging.
4. Celanese Corporation An American chemical company that specializes in the production of PBR and other thermoplastic resins. The company's products are used in various applications, including automotive, electronics, and consumer goods.
Applications of PBR Roll Formers
PBR roll formers are widely used in the production of various plastic products, including
1
Applications of PBR Roll Formers
PBR roll formers are widely used in the production of various plastic products, including
1
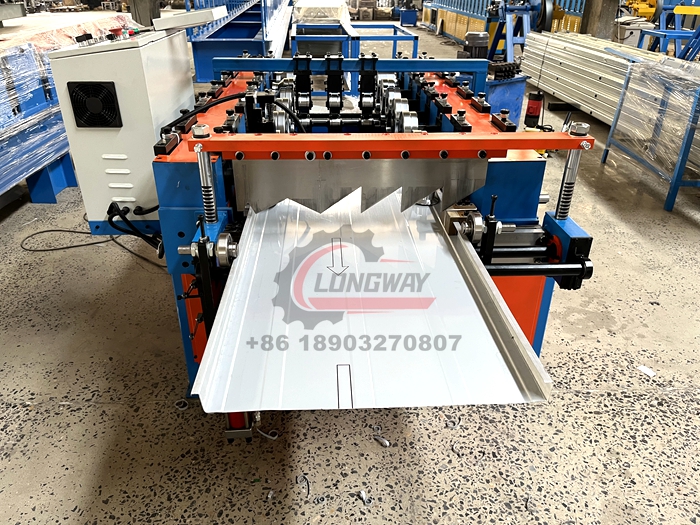
Applications of PBR Roll Formers
PBR roll formers are widely used in the production of various plastic products, including
1
Applications of PBR Roll Formers
PBR roll formers are widely used in the production of various plastic products, including
1
pbr roll former companies. Automotive components PBR is commonly used in the production of automotive components such as bumpers, dashboards, and door panels due to its excellent impact resistance, heat resistance, and chemical resistance.
2. Electrical appliances PBR is also used in the production of electrical appliances such as refrigerators, washing machines, and air conditioners due to its electrical insulating properties and stability at high temperatures.
3. Consumer goods PBR is used in the production of various consumer goods such as toothbrushes, combs, and hair clips due to its durability and low cost.
Future Trends in the PBR Roll Former Industry
The PBR roll former industry is expected to witness significant growth in the coming years due to the increasing demand for high-performance plastics and the expansion of end-use markets. Some of the key trends in the industry include
1. Development of new PBR products with improved properties As the demand for high-performance plastics continues to grow, manufacturers are developing new PBR products with improved properties such as higher heat resistance, lower moisture absorption, and better chemical resistance.
2. Expansion of end-use markets The PBR roll former industry is expected to benefit from the expansion of end-use markets such as automotive, construction, and electronics.
3. Increasing adoption of sustainable manufacturing practices As environmental concerns continue to grow, manufacturers are increasingly adopting sustainable manufacturing practices such as reducing waste, conserving energy, and using renewable resources in the production process.
Conclusion
In conclusion, PBR roll formers play a crucial role in the production of various plastic products. With the increasing demand for high-performance plastics and the expansion of end-use markets, the PBR roll former industry is expected to witness significant growth in the coming years. Manufacturers will need to stay abreast of the latest trends and developments in the industry to remain competitive and meet the growing demand for high-quality plastic products.