The metal roof sheet roll forming machine plays a crucial role in the fabrication of metal roofing systems, offering precision, efficiency, and customization suitable for various architectural applications. As industries and constructions increasingly lean towards durable and sustainable building solutions, understanding and optimizing this equipment’s use becomes paramount, ensuring operational excellence and maximizing return on investment.
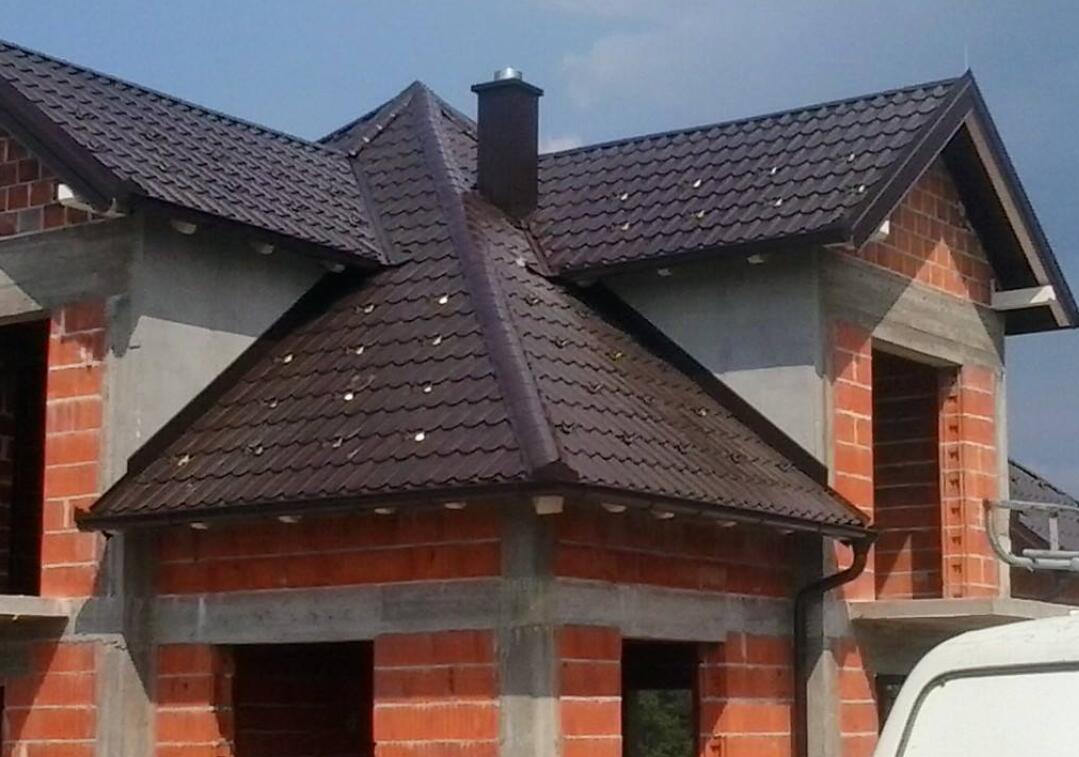
Delving into the operational insights, a metal roof sheet roll forming machine operates by continuously bending a long strip of metal, usually coiled steel, through a sequence of roll stations. Each station makes incremental manipulations to shape the metal precisely into the desired profile. This mechanized approach greatly surpasses traditional methods regarding precision, repeatability, and efficiency, making it a professional necessity for construction entities aiming for scalability and superior outcomes.
The expertise required to operate and optimize these machines involves a comprehensive understanding of both the mechanical components and the technological integrations they house. Modern roll forming machines are equipped with advanced control systems that allow for considerable customization, including programmable logic controllers (PLCs) and human-machine interfaces (HMIs) that streamline operations and reduce downtime. A proficient operator not only commands the technical intricacies but also harnesses real-time data analytics to monitor and adjust processes for optimal performance.
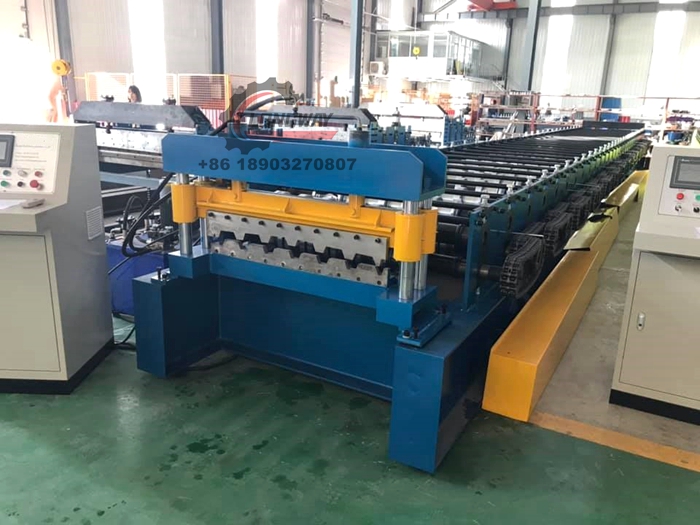
Experience in using a roll forming machine can significantly affect the quality and economic efficiency of the production process. An individual or team with extensive operational history will understand the nuances in machine calibration better, foresee potential malfunctions, and execute timely maintenance. They can adeptly handle material variations and adjust settings to minimize waste, thereby enhancing the sustainability of manufacturing practices. Moreover, understanding the specifics of different metal types and their behavior during the forming process is an asset that ensures quality output tailored to various climatic and structural needs.
metal roof sheet roll forming machine
Adding to the expertise is the machine’s versatility, which allows for the creation of different profiles such as corrugated, trapezoidal, or standing seam panels, catering to a myriad scope of architectural aesthetics and functional demands. This adaptability is crucial in jurisdictions with specific building codes and aesthetic guidelines, thus emphasizing the machine’s pivotal role in innovative building designs. Experts often liaise with architects and engineers to translate visionary designs into practical, manufacturable components seamlessly through the machine.
Authoritativeness in this context extends beyond merely showcasing high-quality machines.
It involves actively contributing to advancements and knowledge dissemination regarding roll forming technologies. Industry leaders often publish case studies, spearhead innovations, and provide training programs to foster a competent workforce conversant with state-of-the-art applications and operational best practices. A roll forming enterprise recognized within professional circles becomes a trusted authority, attracting collaborations and enhancing its market positioning.
Trustworthiness, fundamentally, is built on reliability and customer service excellence. The selection of metal roof sheet roll forming machines typically involves significant capital investment, so stakeholders seek partners who demonstrate consistency in machine performance and post-purchase support. Reputable manufacturers and suppliers are those who extend warranties, offer comprehensive technical support, and maintain transparent communication throughout the machine's lifecycle—from purchase through its operational phase to eventual upgrading or decommissioning.
In conclusion, the value proposition of a metal roof sheet roll forming machine extends well beyond its physical capabilities. It is a convergence of experience-driven operations, expert handling, authoritative innovations, and trust-centered business practices. Stakeholders venturing into metal roofing production must therefore prioritize integrating these machines into their processes with a holistic view, ensuring that every operational, technical, and relational facet is honed to perfection for sustainable success.