The Impact of Rolling on Aluminum Forming
Aluminum, a lightweight and versatile metal, is widely used in various industries due to its excellent properties such as high strength-to-weight ratio, corrosion resistance, and recyclability. One of the most crucial processes in aluminum production is forming, which involves shaping the metal into various forms and sizes. Rolling is one of the most common techniques used in aluminum forming, and it plays a significant role in determining the final quality and properties of the material.
Rolling is a cold working process that involves passing aluminum sheets between two rollers under pressure, causing the metal to deform and achieve the desired shape and size. This process can be applied to aluminum sheets of different thicknesses, ranging from a few micrometers to several centimeters. The main advantage of rolling is that it can produce aluminum products with high dimensional accuracy, smooth surfaces, and uniform mechanical properties.
During the rolling process, the aluminum sheet undergoes severe plastic deformation, which leads to changes in its microstructure. The grain size of the aluminum is reduced, and the grains become more elongated and aligned along the rolling direction. This results in improved strength and toughness of the material, making it suitable for applications that require high mechanical performance.
Moreover, rolling can also improve the surface quality of aluminum products. By controlling the rolling parameters, such as temperature, speed, and reduction ratio, it is possible to obtain aluminum sheets with smooth and shiny surfaces By controlling the rolling parameters, such as temperature, speed, and reduction ratio, it is possible to obtain aluminum sheets with smooth and shiny surfaces
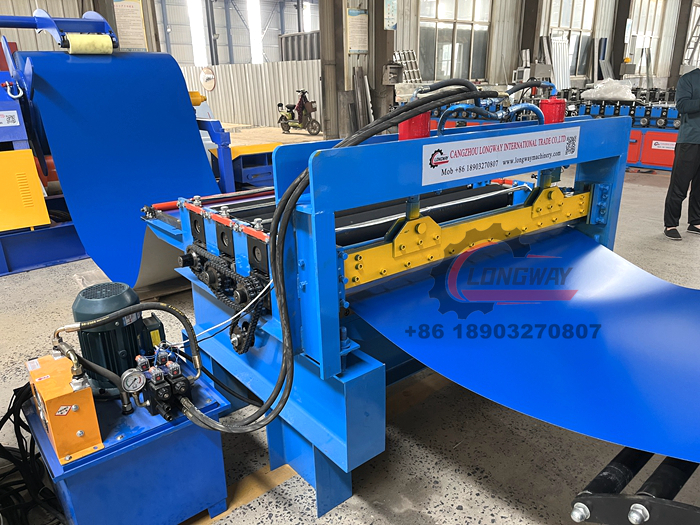
By controlling the rolling parameters, such as temperature, speed, and reduction ratio, it is possible to obtain aluminum sheets with smooth and shiny surfaces By controlling the rolling parameters, such as temperature, speed, and reduction ratio, it is possible to obtain aluminum sheets with smooth and shiny surfaces
roll forming aluminum. This is particularly important for applications where aesthetic appearance is crucial, such as automotive and aerospace industries.
However, rolling also has some limitations. It is generally more suitable for producing flat products, such as sheets and plates, rather than complex shapes. In addition, the rolling process can generate a significant amount of heat, which can lead to thermal stresses and warping of the aluminum sheet. Therefore, it is essential to control the temperature during the rolling process to minimize these issues.
In conclusion, rolling is a crucial process in aluminum forming that plays a significant role in determining the final quality and properties of the material. By controlling the rolling parameters and selecting the appropriate rolling technique, it is possible to produce aluminum products with high dimensional accuracy, smooth surfaces, and excellent mechanical performance. As the demand for lightweight and sustainable materials continues to grow, the importance of rolling in aluminum forming will only increase in the future.