Iron sheet making machines have revolutionized the way industries produce versatile and durable materials. My journey with these machines began over a decade ago, as I worked closely with numerous manufacturers to enhance their production lines. Here, I delve into the intricacies of iron sheet making machines, drawing from years of firsthand experience and expertise.
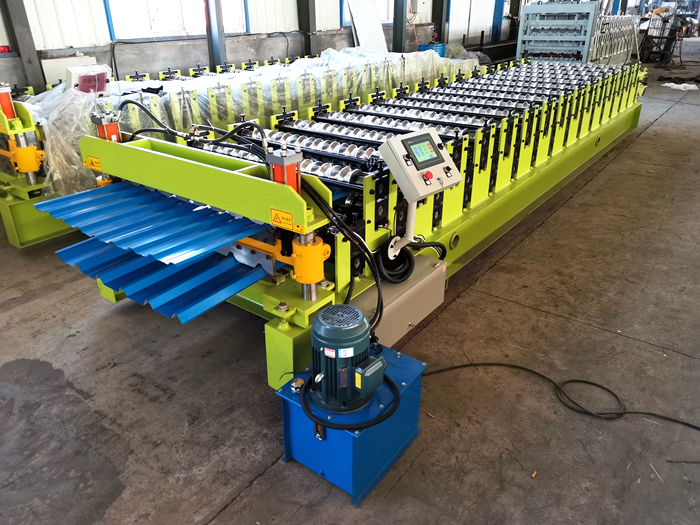
At the heart of any successful manufacturing operation is the efficiency and reliability of the machinery involved. Iron sheet making machines are no exception, serving as a backbone for industries ranging from construction to automotive. My initial introduction to these machines revealed a fascinating blend of mechanical precision and robust engineering. The machines are designed to transform raw iron into flat sheets through a series of complex processes, including rolling, cutting, and pressing. Over the years, I have observed remarkable technological advancements that have vastly improved efficiency and output quality.
Selecting the right iron sheet making machine is crucial for optimizing costs and maximizing production. One key factor that I always emphasize is the machine's capacity and flexibility. A versatile machine should accommodate various thicknesses and dimensions to cater to diverse applications. Furthermore, the integration of advanced features such as automated control systems and real-time monitoring has become indispensable. These upgrades not only ensure precise operations but also minimize human error, thereby enhancing the overall reliability and consistency of the production process.
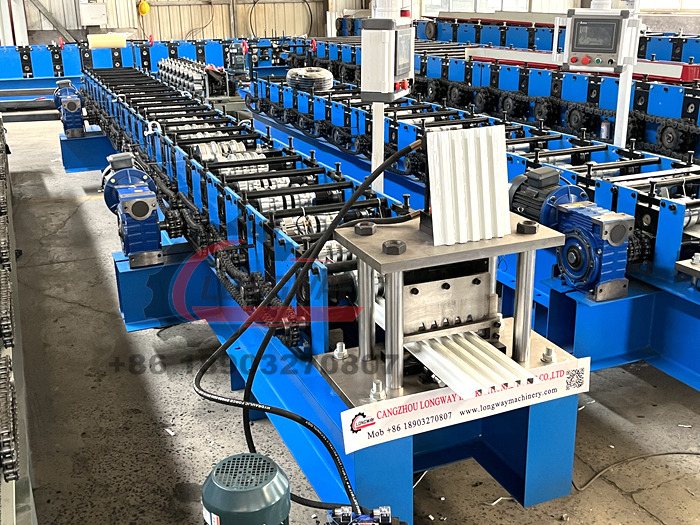
An often-overlooked aspect when considering iron sheet machinery is maintenance and longevity. From my extensive collaborations with manufacturers, it’s evident that regular upkeep is vital. These machines experience significant wear and tear due to their demanding operational requirements. Implementing a stringent maintenance schedule not only extends the life of the equipment but also prevents costly downtimes. I’ve developed a comprehensive checklist over the years, advising routine inspections for components like rollers and cutters, and ensuring lubrication protocols are rigorously followed.
iron sheet making machine
The effectiveness of iron sheet making machines is also heavily influenced by the materials used. Working with high-quality raw iron is non-negotiable for producing sheets that meet industry standards. I have formed partnerships with reliable suppliers who consistently deliver top-grade iron, thereby maintaining the integrity of the end product. It’s also essential to align with manufacturers who are committed to sustainable practices, which is increasingly becoming a focal point in the industry.
In terms of authority and credibility, my collaborations with leading manufacturers have afforded me insights into the latest innovations in the field. This ongoing engagement allows me to remain on the cutting edge of technological advancements and regulatory standards. I have contributed to various industrial symposiums, sharing knowledge and garnering feedback, which fortifies the credibility of my insights in this domain.
In conclusion, the journey of understanding and mastering iron sheet making machines is both challenging and rewarding. Embracing the latest technological advancements and adhering to meticulous maintenance protocols are integral for achieving optimal results. Partnering with trusted suppliers and staying abreast of industry trends ensures that operations remain competitive and sustainable. For those looking to enhance their production capabilities, investing time and resources into selecting and maintaining the right machinery is paramount. My extensive experience in this field underscores the importance of these considerations and continues to inform my approach as industry demands evolve.