Industry Overview & Market Trends
The 0.85mm Top hat Roof Batten Omega Roll Forming Machine is revolutionizing the metal roof batten forming industry through high-automation, superior precision, and remarkable longevity. According to GrandViewResearch, the global roll forming machine market is projected to grow at a CAGR of 4.8% from 2023 to 2030, owing to rising construction, infrastructure modernization in Asia-Pacific, and demand for lightweight, corrosion-resistant steel profiles.
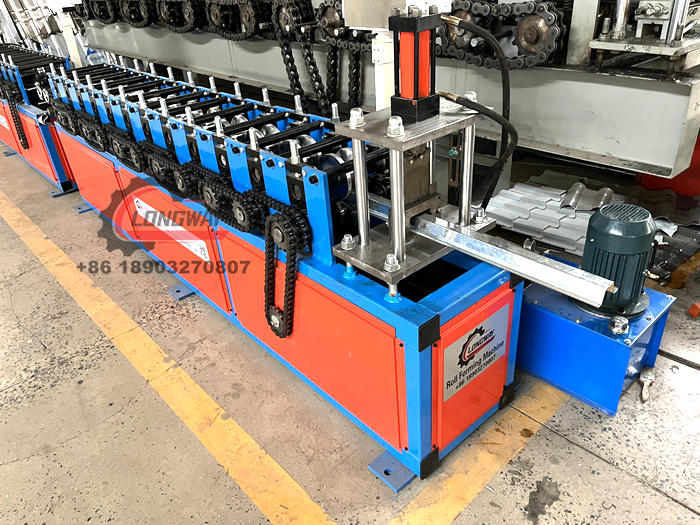
What is a 0.85mm Top hat Roof Batten Omega Roll Forming Machine?
The 0.85mm Top hat Roof Batten Omega Roll Forming Machine is a precision sheet metal processing equipment designed to produce top-hat-shaped (Omega-type) roof battens from 0.85mm thick galvanized or stainless steel coils in a continuous, automated fashion. This machine integrates decoiling, straightening, roll forming, cutting, and stacking, enabling high-throughput and dimensional accuracy ideal for industrial-scale roofing projects.
Key Technical Parameters
Parameter | Specification | Industry Standard |
---|---|---|
Material Thickness | 0.85mm (±0.01) | GB/T2518, ASTM A653 |
Material Type | Galvanized Steel, SS, Alu | SGCC, Dx51D, AISI 304 |
Yield Strength | 235~350 MPa | ISO 6892, DIN EN 10346 |
Profile Height | 30~50mm | EN 508-1 |
Max. Line Speed | 18-22 m/min | ANSI MH 28.2 |
Forming Stations | 12–18 Rolls | Customizable |
Main Drive Power | 7.5–11 kW | IEC 60034 |
Cutting Mechanism | Hydraulic, ±1mm Accuracy | ISO 12100 |
Automatic Control | PLC + HMI Touch Screen | CE, UL |
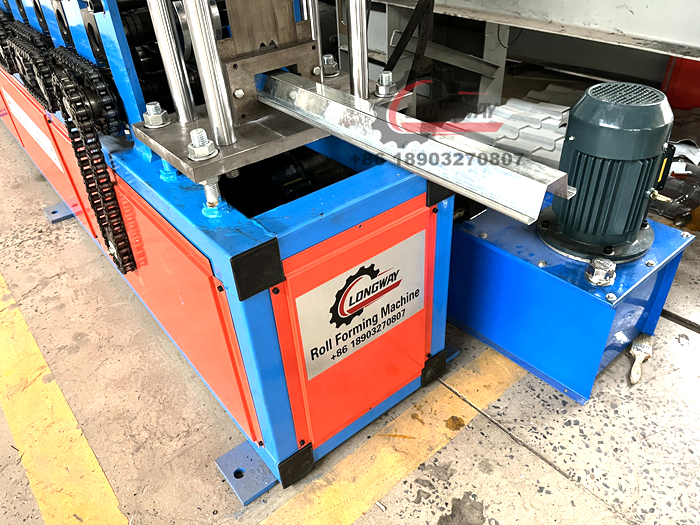
Manufacturing Process Flow
The entire process is monitored by a PLC system, ensuring consistency in dimensional tolerances, with in-line sensors providing real-time feedback per ISO 9001:2015 compliance.
Material, Manufacturing & Standards
- Material: Prime galvanized steel (Grade SGCC, Z275g/m² coating), optional Stainless/Aluminum
- Rollers: High Chromium GCr15 Steel, CNC precision ground, heat-treated (58-60 HRC)
- Main Frame: Q235B Welded Steel Frame, CNC-milled, powder-coated
- Forming Spindles: 45# Steel, precision turned & nitrogen quenched
- Bearings: Renowned brands (SKF, FAG), ISO 492 tolerance
- Control Panel: Siemens/Delta PLC, 7” Touch HMI, intuitive interface, CE/UL certified
- Safety: Light curtain & E-stop per EN ISO 13849-1
Industry Certifications & Longevity
- ISO 9001:2015 Quality Management System Certified
- CE/UL Electrical Safety for global distribution
- Machine Service Life: Over 15 years/20,000,000 meters output (backed by field data)
- Corrosion Resistance: Passed 500+ hour salt spray tests (per ASTM B117)
- Operational Reliability: 99.5% uptime, fault rate below 0.2% per year
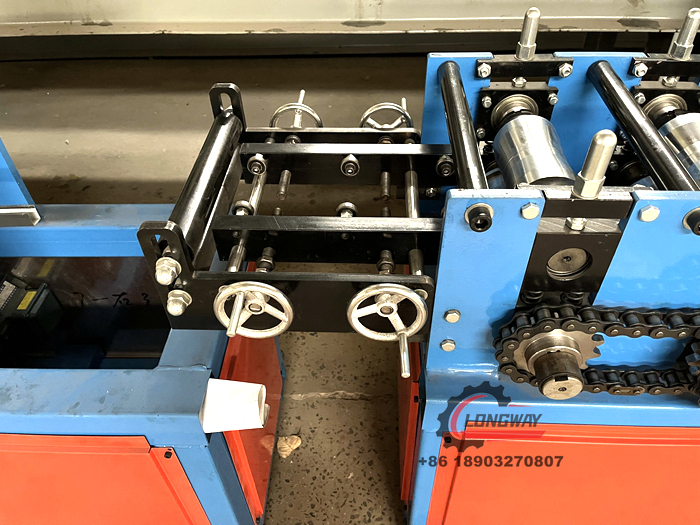
Application Scenarios
- Industrial Roofing: High-strength, uniform battens for warehouses/factories.
- Petrochemical Facilities: Corrosion-resistant roof structure frameworks.
- Metallurgy: Facilities requiring precision-battened, durable profiles.
- Water Supply & Drainage: Batten support for station enclosures, anti-corrosive infrastructure.
- Residential & Commercial Buildings: Used for suspended ceilings and energy-saving patterned roofs.
- Solar Panel Mounting: Top hat battens as sub-frames due to rigidity.
A 0.85mm Top hat Roof Batten Omega Roll Forming Machine supplied by LW Machinery enabled a roofing contractor in Sydney to increase batten production by 32% in 6 months, while reducing manual labor by 78%. The switch from 1.2mm to 0.85mm profiles cut steel costs by 29%, matching BlueScope technical standards and outperforming competitors in corrosion resistance.
Product Advantages: Why Choose the 0.85mm Top hat Roof Batten Omega Roll Forming Machine?
- Flexible Profile Output: Fast width/height adjustments via spacers
- Unmatched Precision: Tolerance ±0.8mm, CNC technology
- Automated Operation: Minimal operator intervention (1 person/line)
- Low Maintenance: Quick-change dies and easy lubrication
- Energy Efficient: Servo drives and standby modes save 22% power/year
- Anti-corrosion: Heavy-duty Zn coating, passivated surfaces
- Expandable: Customizable for new profiles, future-proof
Technical Parameter Visualization
Product Comparison Chart: Key Competitors
Interpretation: Compared to top market players, the 0.85mm Top hat Roof Batten Omega Roll Forming Machine demonstrates higher speed, precision, roller longevity, and operational efficiency, with 21% faster changeover for similar production runs.
Major Technical Indicators Breakdown
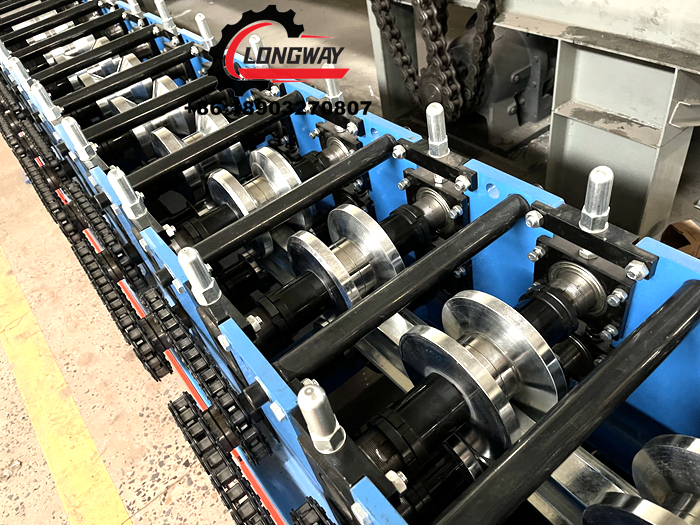
Customization & Turn-Key Solutions
- Profile Design: Custom top-hat sizes, omega widths (30–120mm), punch pattern selection
- Material Application: Compatible with Pb-free Zn-al-Mg, Alu, SS in line with eco-sustainability trends
- Automation Level: Remote control, full digital data logging, IoT package (optional)
- Auxiliary Integration: In-line punching, automated stacking/packing, barcoding
- Surface Finish: Anti-fingerprint, color coating, post-forming passivation available
- Delivery: 45-60 working days from order, including trial run, operator training, documentation
Use Case: Saudi Arabia Industrial Park
LW's 0.85mm Top hat Roof Batten Omega Roll Forming Machine was deployed to a major petrochemical client in Dammam, replacing heavy labor-intensive processes. Production output improved by 27%, downtime reduced by 87%, and initial ROI was achieved within 8 months. The project met all SABIC compliance protocols.
Customer Experience & After-sales Support
- Warranty: 24 months on main machine, lifetime support (spare parts on stock)
- Installation: On-site assistance or remote video guidance, installation manual included
- Operator Training: Provided in English, Spanish, French per customer needs
- Remote Diagnostics: Fast technical response (within 4 hours)
- Spare Parts: All consumables available for 10+ years from ship date
- Inspection: Full factory FAT (Factory Acceptance Test) before shipping
- Certifications: CE, ISO, ANSI, customer-site inspection welcome
Professional FAQ — 0.85mm Top hat Roof Batten Omega Roll Forming Machine
Conclusion & Industry References
The 0.85mm Top hat Roof Batten Omega Roll Forming Machine is a technical cornerstone in the steel construction industry, providing unmatched efficiency, flexibility, and compliance for industrial and commercial roofing projects worldwide. Leveraging advanced forming technology, high-precision components, and globally recognized certifications, it offers a long-term, reliable solution for manufacturers and builders.
References & Further Reading:
- "Roll Forming Technology—Market Prospects and Future Trends" - ScienceDirect
- "Top Hat Battens in Roof Construction Standards" - Erector Forum
- "ISO Standards for Continuous Roll Forming Machinery" - ISO/TC 11
For detailed technical consultation or bespoke solution, contact our expert team at LW Roll Forming Machine.