Roll forming aluminum has revolutionized the manufacturing sector, offering unmatched precision and efficiency for creating complex profiles. This advanced metalworking process involves the continuous bending of long aluminum strips, passing them through consecutive sets of rollers, each performing incremental changes, to achieve a desired cross-section. As a result, roll forming provides numerous advantages that appeal to diverse industries such as automotive, construction, and aerospace, among others.
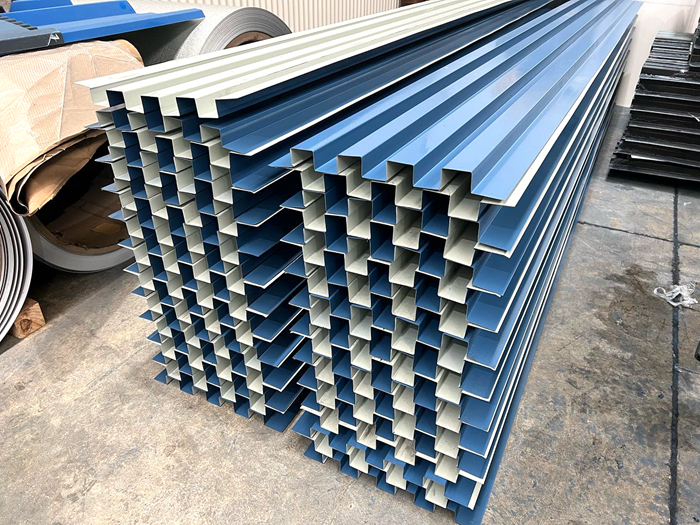
In the automotive sector, the lightweight nature of aluminum makes roll forming an attractive option. The increasing demand for fuel-efficient vehicles necessitates the reduction of overall vehicle weight without compromising safety and performance. Roll forming aluminum allows manufacturers to produce lightweight yet robust components including bumpers, roof rails, and door frames. Its precise engineering also ensures consistency in shape and dimensions, contributing to enhanced aerodynamics and improved fuel economy.
The construction industry benefits significantly from roll forming aluminum due to its ability to fabricate building materials with intricate shapes, such as roofing sheets, structural beams, and wall claddings. This process not only allows for cost-effective mass production but also supports sustainable building practices. Aluminum is highly recyclable, and its adaptability to various designs and finishes makes it suitable for modern architecture. Additionally, the durability and corrosion resistance of aluminum extrusions contribute to long-lasting structures, reducing maintenance demands over time.
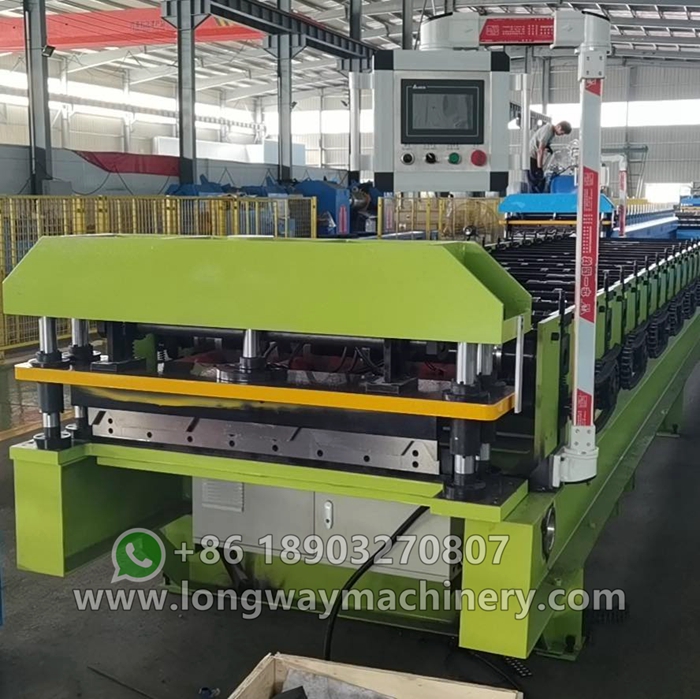
For the aerospace industry, where precision and material performance are paramount, roll forming aluminum presents a solution that meets stringent regulatory standards. Aircraft demand components that are not only lightweight but also capable of withstanding extreme conditions. Precision roll forming fulfills this necessity by creating complex profiles used in fuselage sections, wing structures, and seat tracks, which are engineered for both strength and efficiency. The ability to produce customized shapes and standardized dimensions enhances assembly accuracy and operational safety.
roll forming aluminum
A standout feature of roll forming is its cost-effectiveness. By facilitating automated high-speed production and minimizing waste materials, roll forming allows manufacturers to reduce operational costs significantly without compromising quality. The ability to coalesce multiple production phases into a singular automated operation not only saves time but also increases output, thus providing a competitive edge in market delivery timelines.
Furthermore, technological advancements have propelled roll forming capabilities into new realms. Innovations in computer-aided design (CAD) and roll forming simulation software have enhanced the ability to predict product behavior, optimize tool design, and troubleshoot potential issues prior to production. This integration of technology not only refines precision but also elevates the overall quality and performance of aluminum products.
The expertise and reliability of companies specializing in roll forming aluminum are pivotal to ensuring customer satisfaction and operational success. A commitment to stringent quality assurance protocols and adherence to industry standards fortify trustworthiness in manufactured products. In-depth knowledge of material characteristics, tooling, and mechanical behavior further reinforces authority and excellence within the field.
Roll forming aluminum stands as a beacon of innovation in the realm of manufacturing, merging economic viability with exceptional material characteristics. Its impact across diverse industries highlights its versatility and paramount importance in modern production processes. As the demand for lightweight, durable, and sustainable materials continues to escalate, roll forming will undoubtedly remain a cornerstone in advancing material engineering and product development.