Innovations in the realm of metal processing have consistently driven the construction and manufacturing industries forward, and the metal wall panel roll forming machine is a testament to that progress. These machines, intricate in design yet astonishingly efficient, transform flat sheets of metal into robust wall panels, used in a variety of applications from commercial buildings to residential homes. This article delves into the nuances of this remarkable technology, highlighting its essential features, advantages, and the reasons it stands as an indispensable asset in modern industry.
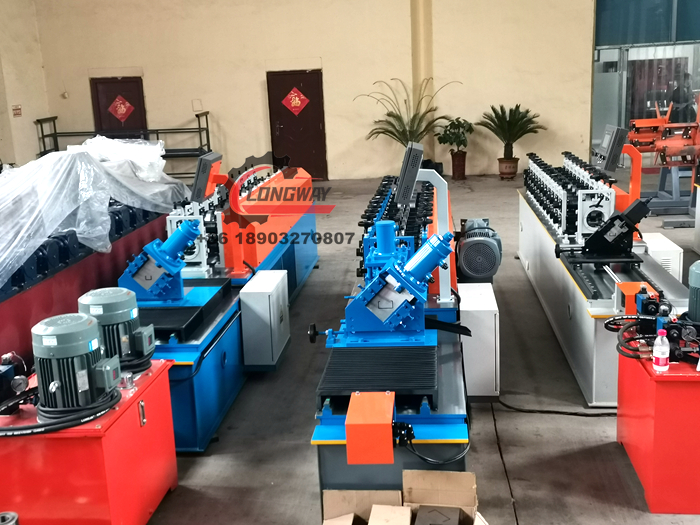
Precision and Expertise at Work
Metal wall panel roll forming machines are engineered with precision in mind. These machines incorporate advanced roller systems that meticulously shape metal sheets with exacting accuracy. The expertise behind designing these roller profiles is commendable, as each roller must be engineered to handle different types of metal, thicknesses, and dimensions. Professionals in the industry agree that the intricate interplay of rollers, guides, and sequential operations ensures that every panel produced meets stringent quality standards, proving the machine's prowess in precision engineering.
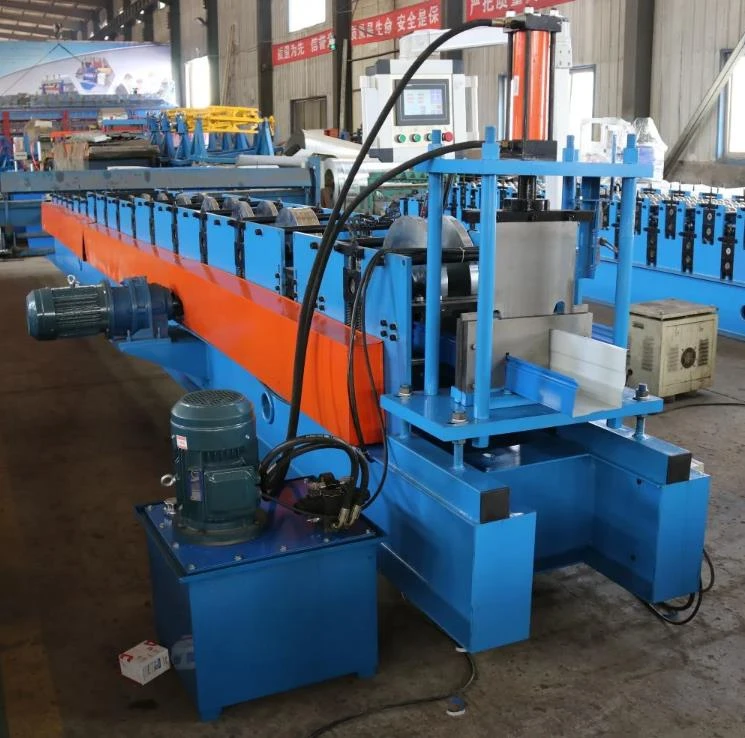
Unmatched Production Efficiency
Efficiency is a hallmark of these machines. Capable of producing panels at remarkable speeds, they cater to high-volume demands without compromising on quality. This scalability is crucial for construction companies facing tight deadlines or large projects. Automated processes minimize human error and labor costs, while continuous feeding systems reduce downtime, making roll forming machines both time and cost-efficient. This high throughput, coupled with lower operational expenses, underscores why businesses consider these machines an investment with promising returns.
Adaptability and Versatility
One of the standout features of metal wall panel roll forming machines is their adaptability. They are versatile enough to accommodate a variety of designs, from simple to complex profiles, fitting the diverse aesthetic and functional requirements of different projects. This versatility extends to materials as well, with machines handling a range of metals such as steel, aluminum, and galvanized sheets. Such flexibility ensures that businesses can meet unique client specifications without necessitating costly equipment changes.
metal wall panel roll forming machine
Reliability Building Trust in Technology
The reliability of metal wall panel roll forming machines breeds trust. Manufacturers have established authority in the field through years of innovation and refinement, creating machines that deliver consistent performance. Regular maintenance and advancements in technology have reduced breakdowns, ensuring that the production line remains dependable. This reliability is further backed by warranty offerings, technical support, and customer service provided by manufacturers, enhancing the trustworthiness of these machines.
Commitment to Quality and Safety
Safety standards are paramount in the operation of roll forming machines. Built with protective guards and emergency stop systems, these machines ensure a safe working environment, demonstrating a commitment to employee safety. Additionally, their design supports the consistent quality of output. Unlike traditional methods, the precision of roll forming machines ensures that each metal panel adheres to exact specifications, reducing wastage and ensuring a high-quality end product.
Environmental Considerations
In an era where sustainability is increasingly prioritized, metal wall panel roll forming machines offer ecological benefits. The accuracy and efficiency of these machines minimize material waste, and the durable panels they produce contribute to longer-lasting structures, reducing the frequency of replacements. Furthermore, metal panels are recyclable, aligning with sustainable practices in construction.
In conclusion, the metal wall panel roll forming machine is a cornerstone technology that harmonizes efficiency, precision, and versatility. Its adoption can significantly benefit industries seeking to enhance productivity while maintaining high standards of quality and sustainability. As the demand for innovative construction solutions grows, the role of these machines in shaping the future of metal processing becomes even more pronounced. By investing in such reliable and advanced equipment, businesses not only elevate their operational capabilities but also fortify their reputation as leaders in the industry.